New government regulations are quickly changing how companies can operate. Common operating principals driving decisions are:
1) protecting employees and their families
2) protecting facilities
3) continuing to serve customers.
In order to re-open, factories are adapting processes to keep workers at least 6 feet of each other. Many companies will require workers to keep at least 6 feet of one another. This new mandate directly impacts processes throughout the factory including semiconductor device programming.
Reduced labor and Floor Space Costs
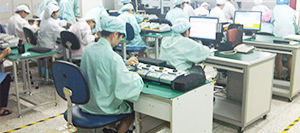
Rising labor rates, shrinking semiconductor flash, and microcontroller device packages, as well as the risk of human error, have already accelerated the move from manual to automated device programming. In a COVID-19 world, transitioning to automated programming is more critical than ever. A manual programming process in factories typically has tens to hundreds of employees sitting in rows of close proximity – a high risk for contagion in today’s environment.
To mitigate risk, companies are transitioning from manual to automated programming to support social distancing inside the factory and reduce the risk of the spread of infection. One operator can typically support 3 automated programming systems. Each system can support programming volumes from 10’s of thousands to millions of devices per year. As volumes ramp companies can expand the capacity of their existing systems to program more devices or purchase an additional system. Each automated programming system is typically spaced more than 6 feet apart.
Higher Quality
Automating device programming is the key to producing higher-quality products by reducing human errors and improving consistency and accuracy. With many manual steps in the process of semiconductor device programming, you are faced with a multitude of opportunities that can lead to defects, but with automation, you eliminate human process errors such as mis-programmed parts, blank parts, and coplanarity errors that you may not discover until after the part is soldered on the PCB. The high visibility from automated device programming allows you to detect and correct programming errors before they reach the assembly and test steps downstream. There are 40 typical problems associated with manual programming. By switching to automated programming, you solve 36 of those problems and the remaining 4 are resolved through process control software.
Automated programming delivers higher-quality programming results. Taking the time to ensure you are delivering quality products will only contribute to your long-term customer satisfaction, retention, and revenue. Challenges associated with manual handling of small parts include ensuring pin 1 orientation is correct going into the socket, the risk of bumping a tray and scattering parts, and lost parts. These challenges are even more apparent when handling small devices manually. Companies who remain using manual programming continue to use extra time and resources to solve approximately 40 typical problems. While others who have made the switch to automated programming solutions have reduced their time and costs by minimizing work-in-process in the supply chain, increasing programming yield quality, and reducing labor costs by having one operator support 3 systems at a time. Data I/O provides the lowest total cost in automated programming so that you can focus on powering the world to be connected at a distance.
Automated Programming Delivers The Lowest Total Cost
Did you know that automated programming can deliver the lowest total cost? A common misconception is that manual processes are cheaper than automated. This is especially prevalent in low-cost regions around the world where labor is calculated as the primary expense. However, below the surface are hidden costs that drive up the overall cost of manual programming including:
- Damaged or incorrectly programmed devices for scrap, rework & returns
- Extra inventory
- Warranty / Service costs
These additional costs are directly correlated to quality issues that are avoided when switching to an automated device programming process.
Data I/O provides the lowest total cost of programming with a family of highly scalable and flexible automated device programming systems to choose from, the industry’s fastest programming technology, and a suite of software options. Keeping cost in mind, your programming strategy can impact the bottom line.
Benefits of Automated Programming
Now is an ideal time to evaluate your microcontroller and flash programming strategy. A manual programming strategy adopted in the past may not be the best solution for today’s world. By being able to have one operator support 3 systems you can easily conduct operations to support programming volumes from 10’s of thousands to millions of devices per year and deliver high quality results by reducing human errors with precision handling. The lowest total cost in automated programming allows you to focus on powering the world to be connected at a distance.
Data I/O offers a suite of automated programming systems to meet your productions, quality and cost requirements. To learn how to transition your factory from manual to automated programming contact us today.
Take our Total Cost of Programming Challenge to learn how much you can save switching to automated device programming.